Our project focused on designing a stable, robust pneumatic robot with smooth turning capabilities. We laser-cut plywood platforms for a lightweight base and used aluminum rods and brackets for added stability. The motion relies on double-acting cylinders and solenoid valves to control airflow, with a compact air reservoir and compressor ensuring consistent pressure.
We implemented a bell-crank mechanism to convert linear pneumatic motion into smooth rotational steering. 3D-printed components enhanced precision, and we centralized key parts to simplify maintenance. An Arduino controlled the actuators, optimizing movements with minimal lag.
The design balanced pneumatics and mechanics, offering smooth motion with careful pressure management and earned us 2nd place out of 200 other students in a competition.
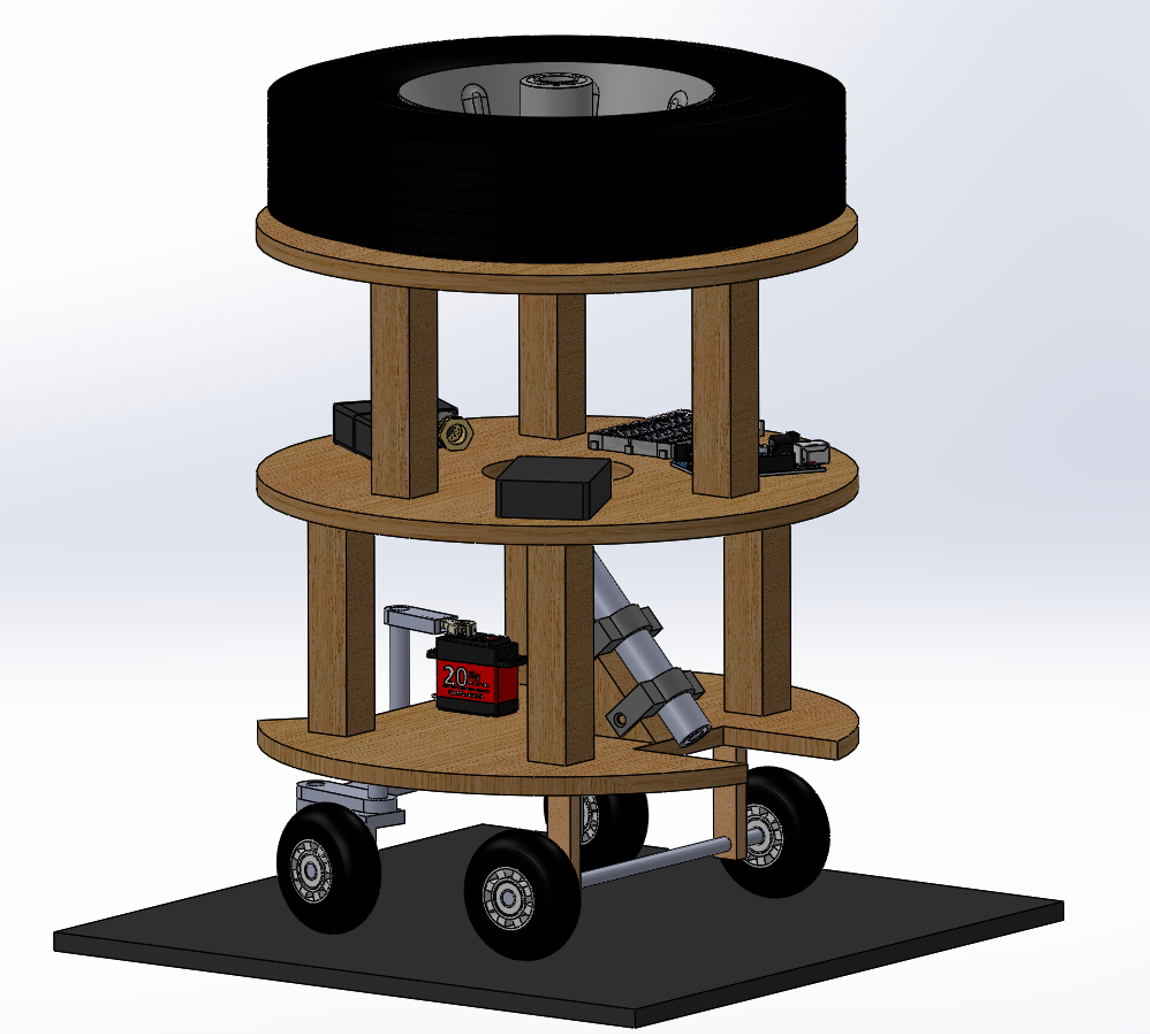
CAD Assembly

Theoretical Impulse Response
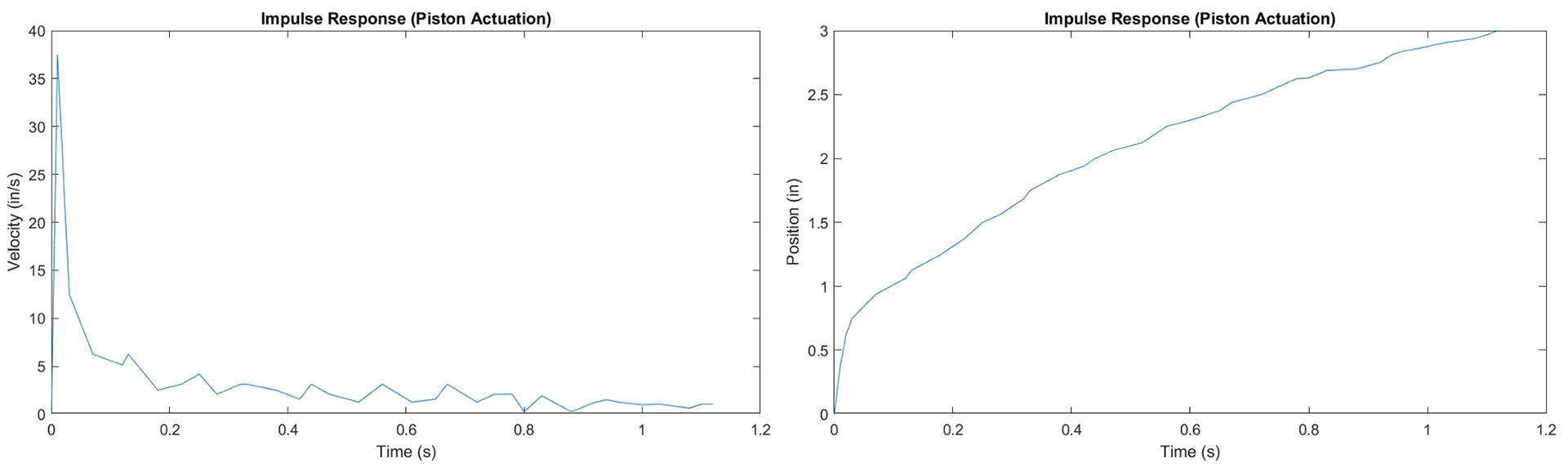
Experimental Impulse Response
When comparing experimental and theoretical data, notable differences emerge. Both data sets exhibit an upward trend, but the theoretical plot is smoother. This discrepancy arises from pressure losses during repeated pneumatic actuations and increased friction from the uneven surface the robot traversed.
Additional factors, such as nonlinearities in the pneumatic system, delays in valve actuation, and small air leaks, further influenced the experimental results.
Environmental variables, including wind resistance, surface irregularities, and tire pressure fluctuations, also affected real-world performance. These discrepancies highlight the limitations of the MATLAB simulations, which assumed ideal conditions and neglected certain practical constraints.
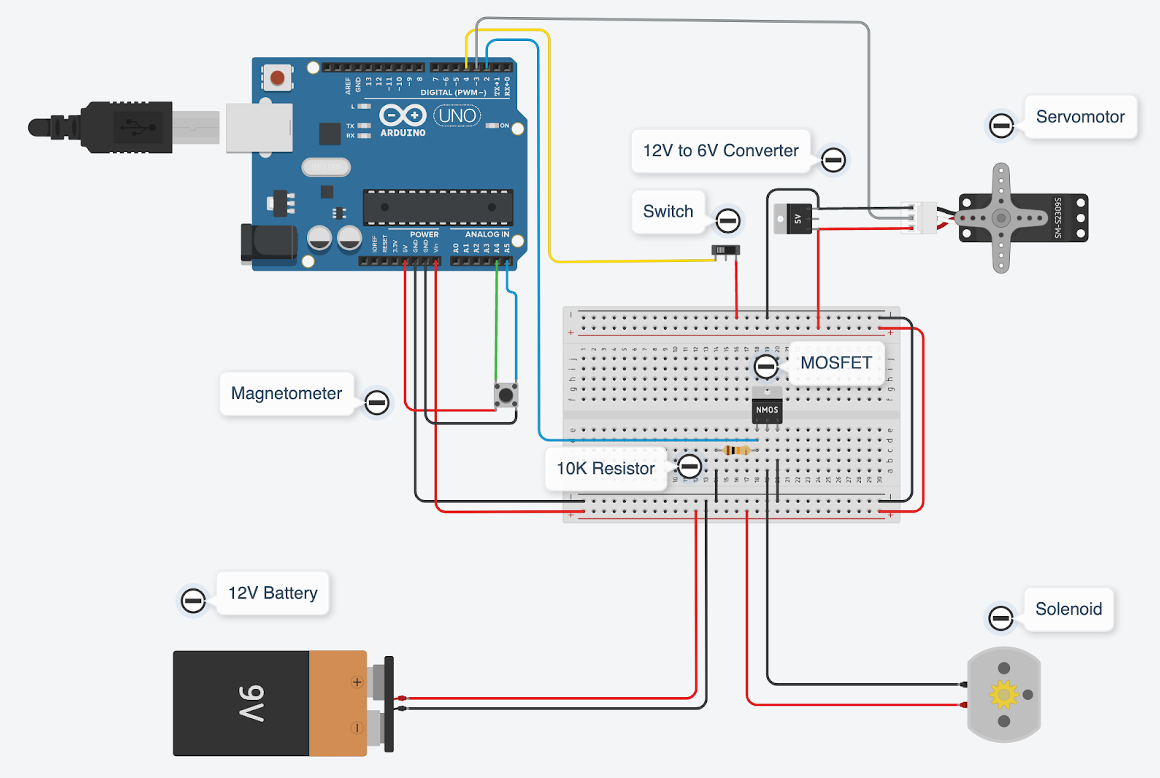
Wiring Diagram
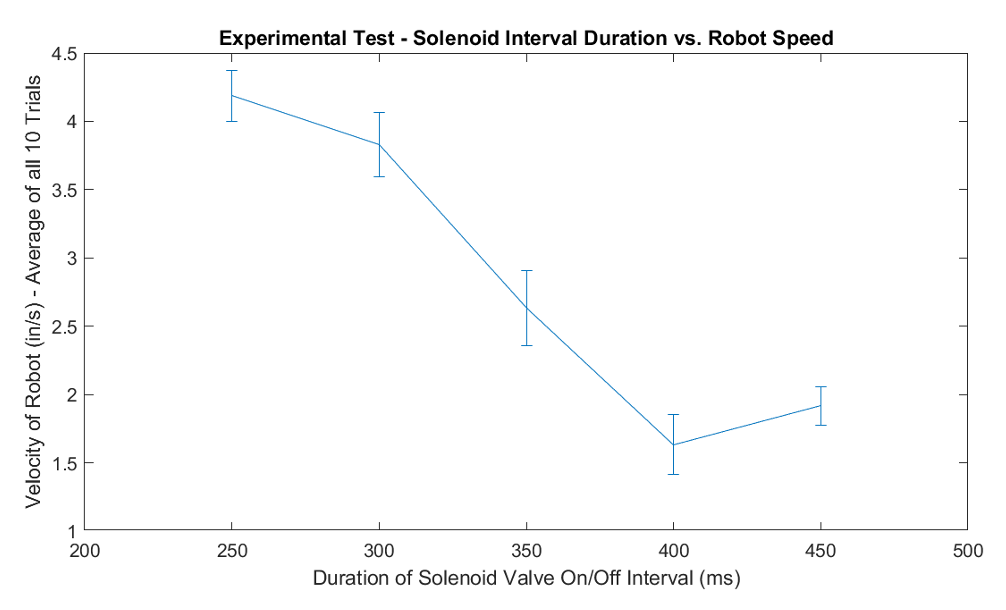
Solenoid Interval Duration vs. Robot Speed
The robot has 1 servo motor that covers 55 degrees of freedom which allows greater maneuverability through the obstacle course.
We found that an interval of 300 milliseconds for the solenoid to turn on and off at was preferred for our robot to move at optimum velocity.