1st Place - 2025 Southwestern Regional Engineering Competition
Inspired by NASA’s Perseverance Rover, this award-winning project delivers an autonomous, flyer-dispensing rover designed to interact with students across UCI’s campus. The rover navigates outdoor terrain, detects bystanders, and uses a vacuum-powered propulsion system to distribute flyers in real-time.
As Lead Mechanical Engineer, I directed a 6-person cross-functional team, owning the full mechanical development cycle—from concept and prototyping to manufacturing and validation. I worked closely with electrical and controls teams to ensure seamless subsystem integration and reduce rework through structured DFM and EOL testing strategies.
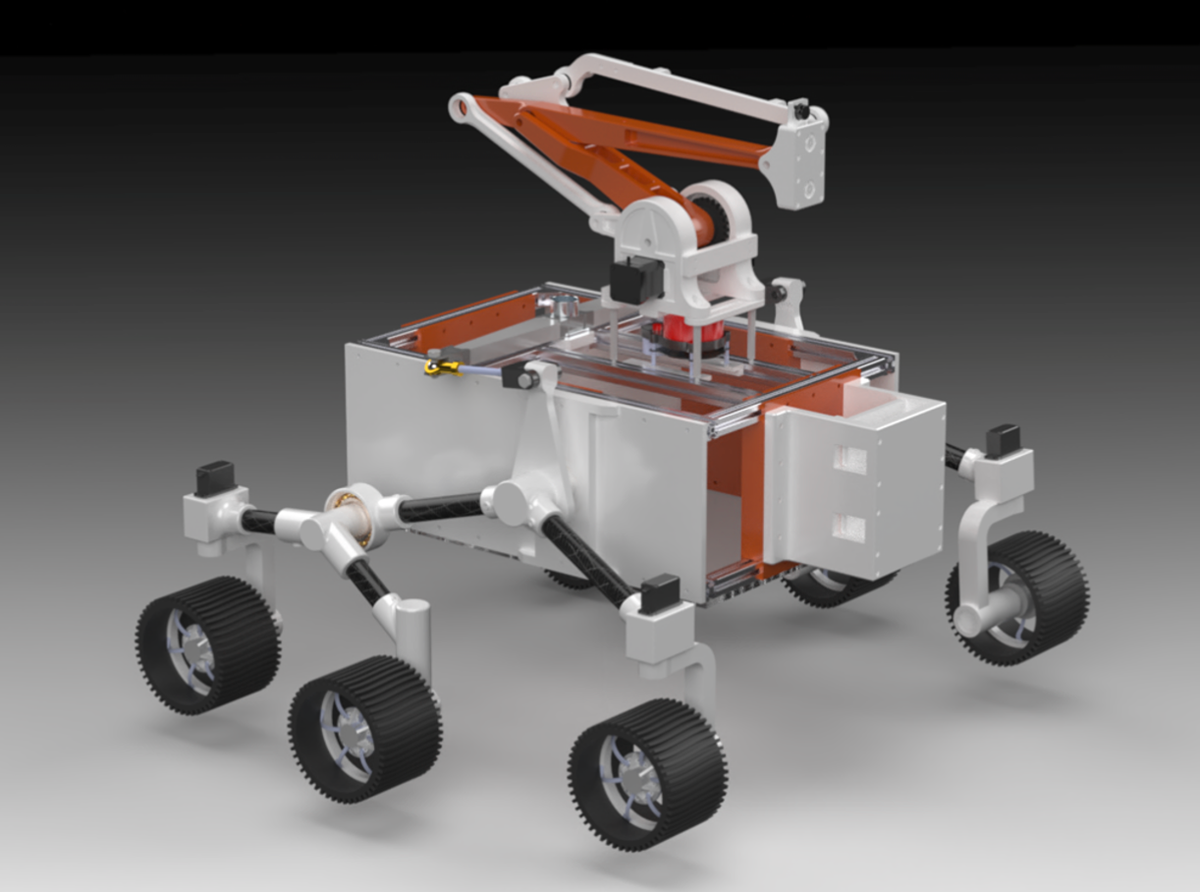
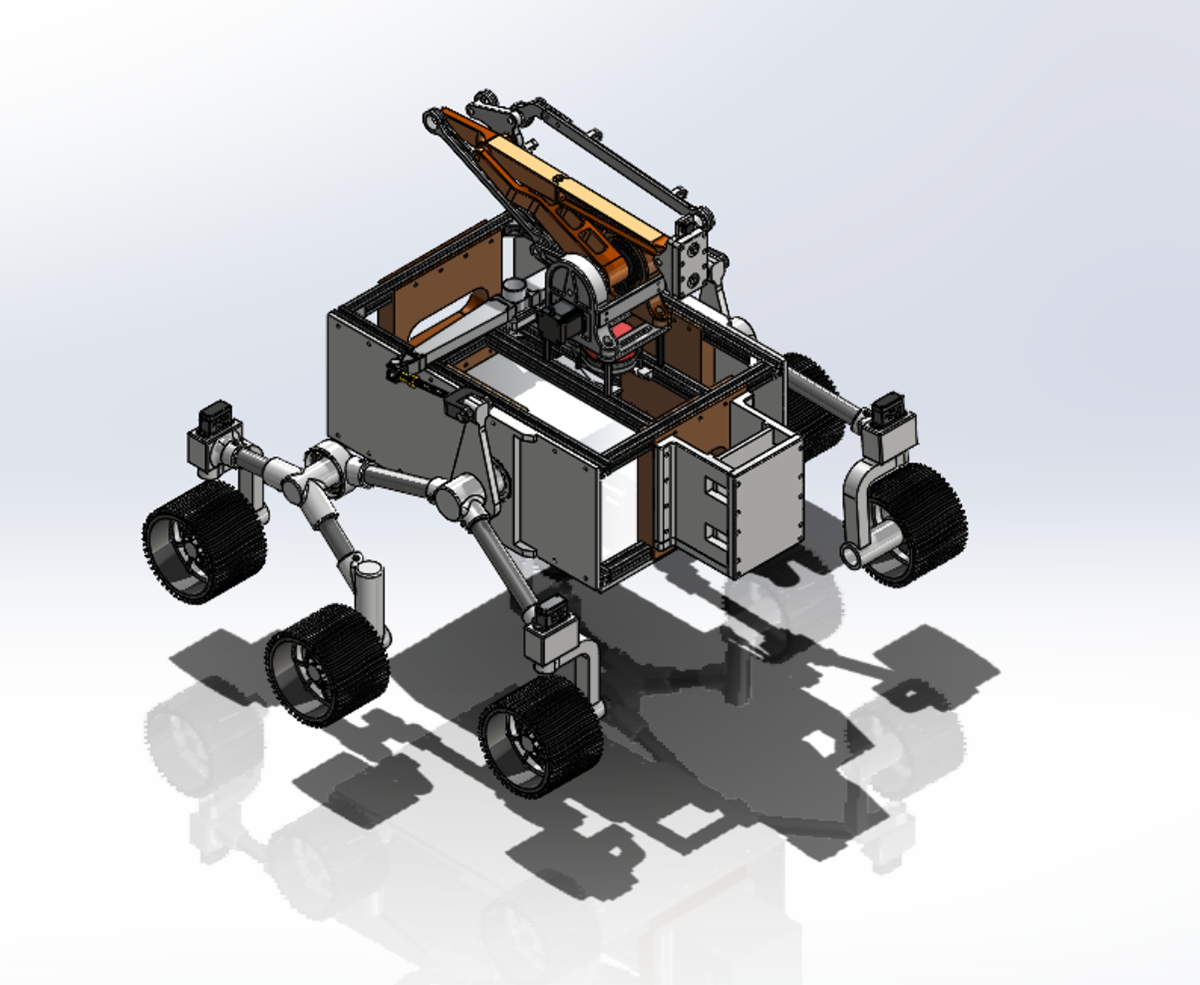
SolidWorks full Assembly
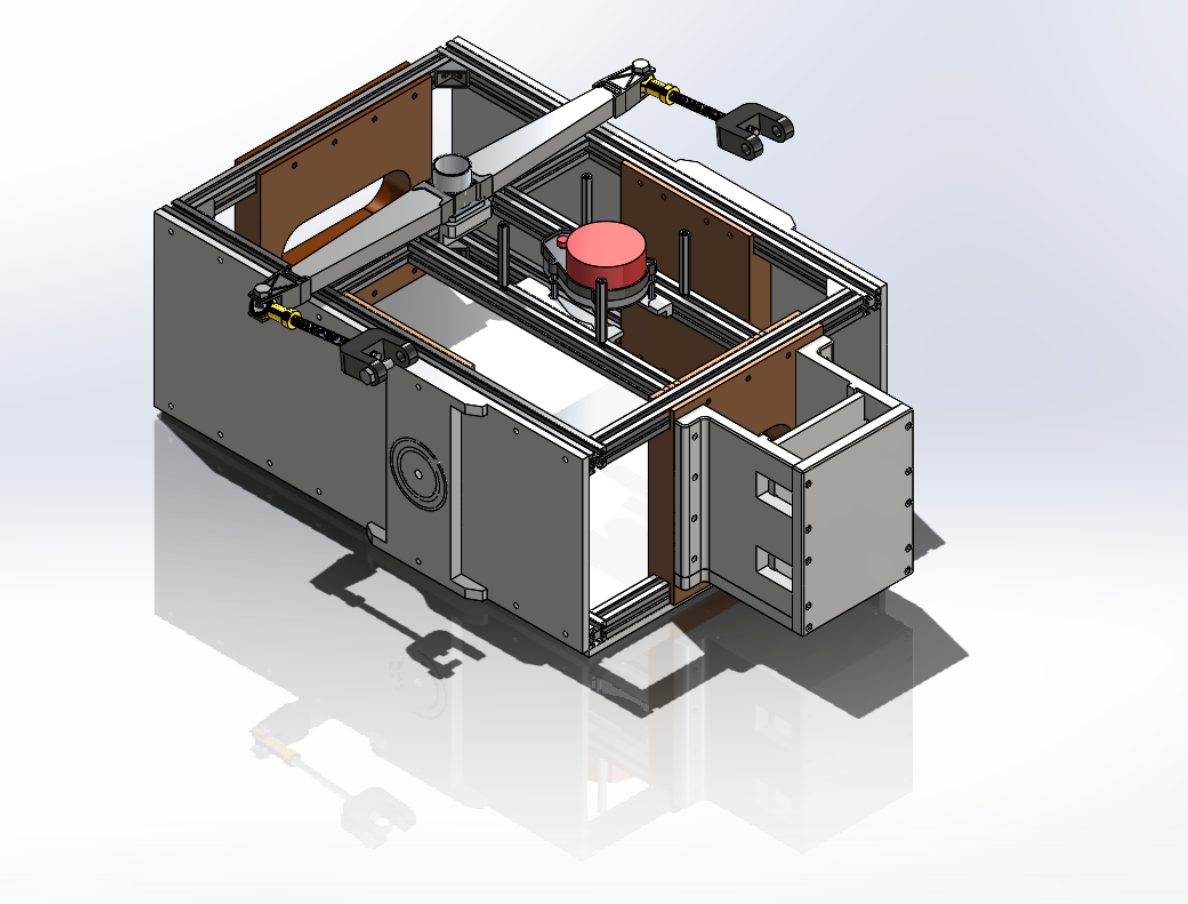
Chassis of Rover
System Design
Led chassis and suspension design using 20x20 aluminum extrusion and HDPE sheeting, balancing durability, weight, and ease of assembly.
Integrated mechanical mounting points for the flyer dispenser, GPS module, and linear bearing slider.
Co-developed a rocker-bogie suspension using parametric SolidWorks sketches for robust terrain adaptability.
Manipulator & Dispenser Development
Aided in Design and manufactured a 2DOF vacuum-powered flyer arm using NEMA 17 stepper motors and a custom gear train.
Used MATLAB and Simulink to simulate linkage geometry and torque loads (0.8 Nm), optimizing dispenser height and stability.
Implemented integrated limit switches, encoder tracking, and a sealed PETG air manifold for precise and repeatable flyer delivery.
Manufacturing & Integration
Led DFM efforts that reduced fabrication and assembly time by 40%; oversaw manufacturing using 3D printing, laser cutting, and CNC machining.
Authored detailed assembly drawings and exploded views in SolidWorks for cross-subteam collaboration.
Coordinated mechanical-electrical integration across subteams, ensuring subsystem compatibility and signal routing without EMI interference.
Testing, Validation & Competition
Simulated EOL test conditions during integration to verify mechanical readiness before competition.
Conducted functional testing of arm movement, wheel articulation, and vacuum delivery under real-world constraints.
Presented system functionality and won 1st Place at the 2025 Southwestern Regional Engineering Competition, outperforming 20+ interdisciplinary teams.
Tools & Technologies
CAD & Simulation: SolidWorks, SolidWorks Simulation, MATLAB, Simulink
Manufacturing: 3D Printing (PETG), CNC Machining, Laser Cutting
Controls & Embedded: ESP32, Arduino Mega, UART, I2C, Limit Switches
Actuation: NEMA 17 Stepper Motors, Vacuum Pump, Servo Motors
Project Tools: BOM Tracking, Tolerance Stackups, Technical Presentation